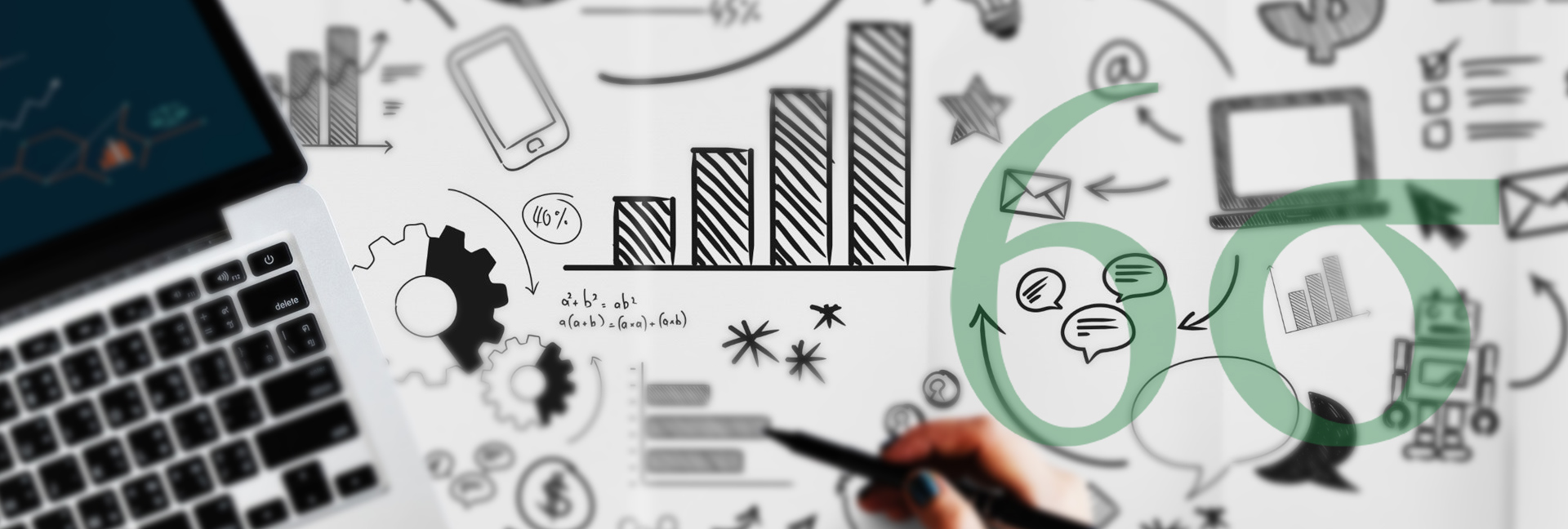
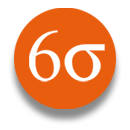
Six Sigma - Produkt- und Prozessoptimierung
Six Sigma Produkt- und Prozessoptimierung
Six Sigma (6σ) ist ein Managementsystem zur Prozessverbesserung, statistisches Qualitätsziel und zugleich eine Methode des Qualitätsmanagements. Ihr Kernelement ist die Beschreibung, Messung, Analyse, Verbesserung und Überwachung von Geschäftsvorgängen mit statistischen Mitteln. Dazu kommt häufig die Define - Measure - Analyze - Improve - Control (DMAIC)-Methodik zum Einsatz. Die Ziele orientieren sich an finanzwirtschaftlich wichtigen Kenngrößen des Unternehmens und an Kundenbedürfnissen.
Six Sigma als Standardabweichung
Der Begriff Sigma wird oft als Maßstab für Fähigkeit, Ertrag und Qualität verwendet. Verwenden Sie diese Skala, entspricht Six Sigma einem Fehlerpotenzial von 3,4 Fehlern bei einer Million Möglichkeiten (DPMO). Daher wurde Six Sigma ursprünglich als Fehlerreduzierungsprogramm entwickelt und zunächst in der Fertigungsindustrie - später auch im Dienstleistungssektor -angewendet.
Six Sigma als Methodik
Six Sigma ist eine Methode, welche eine umfassende Auswahl von Werkzeugen bereit hält, um systematische und analytische Verbesserungen oder Neugestaltungen von Prozessen zu realisieren. Six Sigma ist ebenfalls ein statistisches Qualitätsziel und trägt somit entscheidend zur Kundenzufriedenheit und Ertragssteigerung bei.
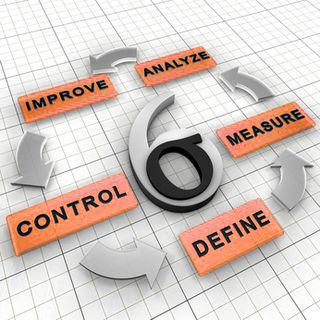
Probleme kann man niemals mit der gleichen Denkweise lösen, durch die sie entstanden sind.
Albert EinsteinUnsere Six Sigma Produkt- und Prozessoptimierung steht für:
- Verstehen und Einhalten von Kundenanforderungen
- Optimierung der Prozesse, um diese elementaren Anforderungen zu erreichen
- Eliminierung von Verschwendung
- Reduktion von Variation
- Steigerung der Effizienz
- Prozessuntersuchung mittels statistischer Analyseverfahren (z.B. mit der Statistiksoftware Minitab)
- Schnelle und dauerhafte Verbesserungen Ihrer technischen- und administrativen Prozesse.
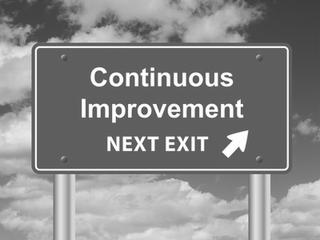
Das Herzstück unserer Methodik ist das DMAIC-Prozessverbesserungsmodell:
- Define: Beschreibung der Aufgabenstellung
- Measure: Prozessfähigkeitsuntersuchung
- Analyse: Untersuchung der Streuungsquellen
- Improve: Reduzierung der Variation
- Control: Prozessüberwachung
Das könnte auch Ihre Six Sigma Erfolgsstory sein:
Ein Unternehmen wirbt für seine neuen Six Sigma Prozesse. Ein Kunde bestellt 950 Teile und sagt: "Wir wollen nicht mehr als 2 fehlerhafte Teile pro 950 Stück". Das Six Sigma Unternehmen versendet 950 Teile termingerecht zum Kunden. Zusätzlich erhält der Kunde ein weiteres kleines Paket. Daraufhin ruft der Kunde den Lieferanten an und fragt: "Was ist in dem Paket?" Die Six Sigma Firma antwortet: "Die 2 fehlerhaften Teile."
Projektrahmen von Six Sigma Projekten:
Six Sigma wird ausschließlich in Form von Projekten umgesetzt. Daher muss der Auswahl für das konkrete Optimierungsprojekt eine besondere Beachtung geschenkt werden. Wir bei PACT Process Solutions bearbeiten Six Sigma Projekte sehr erfolgreich, und das seit mehr als 15 Jahren. Neben unserer sehr erfolgreichen Projektarbeit werden wir von unserer Kundschaft immer wieder gefragt, ob wir vor Ort ein „hands on“ Six Sigma Training mit den Fach- und Führungskräften durchführen können, das hat dazu geführt, dass wir bereits über 150 Six Sigma Green Belts erfolgreich ausgebildet und zertifiziert haben.
Auswahlkriterien:
- Projektlaufzeit: 3 bis 6 Monate
- Projektvolumen: bei großen Unternehmen im Durchschnitt 250.000 €, bei mittelständischen Unternehmen im Durchschnitt 100.000 €
- Projektrahmen: thematisch und organisatorisch abgrenzbar
- Prozessfokus: es liegt ein sich wiederholender Prozess mit einem sich wiederholenden, messbaren Prozessergebnis vor
Auswahlkriterien:
- Projektlaufzeit: 3 bis 6 Monate
- Projektvolumen: bei großen Unternehmen im Durchschnitt 250.000 €, bei mittelständischen Unternehmen im Durchschnitt 100.000 €
- Projektrahmen: thematisch und organisatorisch abgrenzbar
- Prozessfokus: es liegt ein sich wiederholender Prozess mit einem sich wiederholenden, messbaren Prozessergebnis vor
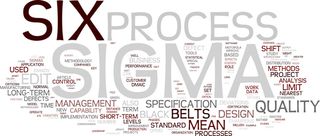
Folgende Erfolgsbilanz lässt sich zügig realisieren:
- Robuste Kosteneinsparung von jährlich: 68 %
- Reduktion der Prozessfehlerhäufigkeit: 66 %
- Steigerung der Kundenzufriedenheit: 44 %