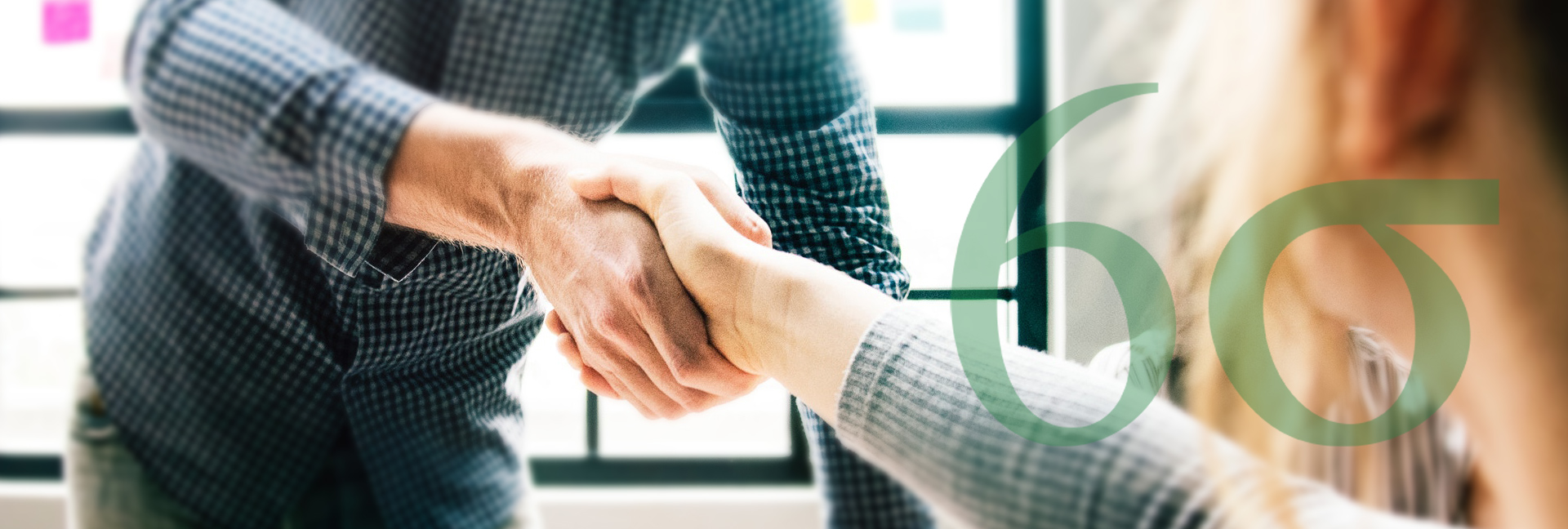
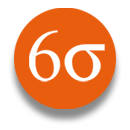
Referenzen unserer Arbeit
„Hands on‟ bedeutet bei uns mittendrin statt nur dabei!
Branchen
Luftfahrt
Automotive
Maschinenbau
Anlagenbau
Logistik
Unternehmen
General Motors
DeLaval Ltda. (Argentina)
Mercedes Benz
Volkswagen
Porsche
Boshoku Automotive Europe GmbH
Toyota, DeLaval Services GmbH
SELL GmbH
Magna Electronics Europe GmbH
GDF Suez, DeLaval Ltda. (Brazil)
Asco Deutschland GmbH
IBS Filtran GmbH
Auswahl einiger Referenz-Projekte
Einführung von LEAN-Logistik in einem globalen Distributionszentrum bei einer Tochter eines weltweit führenden Verpackungsmittelherstellers zur Unterstützung und Einführung des konzernweiten Produktionssystems in der Lagerwirtschaft und Logistik.
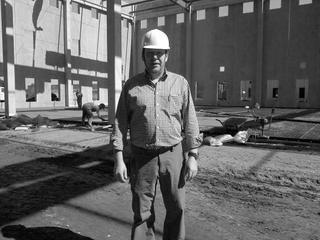
Six Sigma Lean Enterprise Unterstützung zur Erstellung einer Baseline zur Ermittlung von Kosteneinsparpotenzialen in Verbindung mit einer Untersuchung zur Änderung der Organisationsstruktur für die Bereiche Produktion und Instandhaltung. Neben verschiedenen Möglichkeiten zur Organisationsänderung konnten auch signifikante Einsparpotenziale in Millionenhöhe ermittelt werden.
Leitung des Projektes „Verlagerung der Produktion der Einbaugeräte“. Für dieses Projekt wurde eine Produktionshalle angemietet. Diese musste umfangreich renoviert, restrukturiert und nach den neuesten Erkenntnissen der schlanken Produktionsprinzipien organisiert werden. Insgesamt waren durch den Umzug mehr als 90 direkte und indirekte Mitarbeiter betroffen. Für das gesamte Projekt standen nur 6 Monate Zeit zur Verfügung. Das Projekt wurde im Kosten- und Zeitrahmen abgeschlossen.
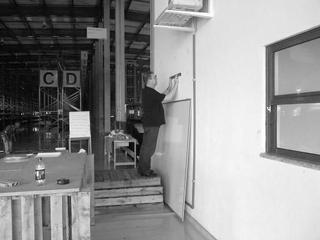
Einführung von Lean-Logistik in Zusammenarbeit mit einem globalen Warehouse Team zur Planung und Umsetzung eines neuen Lager- und Distributionszentrums für den gesamten Lateinamerikanischen Markt (green field) in Campinas / Brasilien.
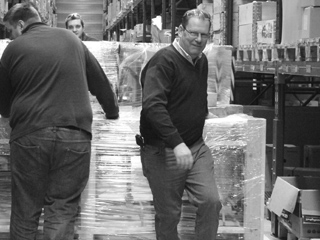
Ausbildung von 36 Six Sigma Green Belts gemäß Anforderungen und in Übereinstimmung mit „operational excellence“ am Standort eines Distributionszentrums zur Sicherstellung und Weiterführung der eingeleiteten Six Sigma und Lean Production Verbesserungsmodelle. Die ausgebildeten und zertifizierten Six Sigma Green Belts konnten bereits Einsparungen in Höhe von € 0,6 Mio. realisieren.
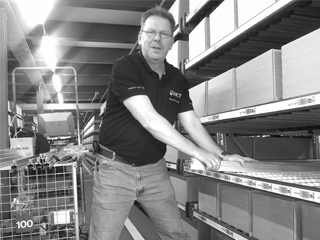
Einführung von Lean Production im Geschäftsbereich Reparatur und Überholung von Hilfsgasturbinen und Triebwerken - Reduzierung der Durchlaufzeiten um 58%, Produktivitätssteigerung um 8%, Lean Benchmark.
Einführung eines durchgängigen Kennzahlensystems zur Steuerung und Überwachung der operativen und administrativen Leistungsparameter. Steigerung der Produktivität um 18% bei gleichzeitig optimierter Synchronisation der operativen und administrativen Geschäftsprozesse.
Six Sigma Black Belt Unterstützung des Projektteams bei der Fehleranalyse plötzlicher und zunehmender Feldausfälle eines Bauteils für die Diesel-Motorensteuerung. Untersuchung und Dokumentation aller Ausfallwahrscheinlichkeiten und Hypothesen. Fortschrittsbesprechung bei Kunden und Lieferanten.
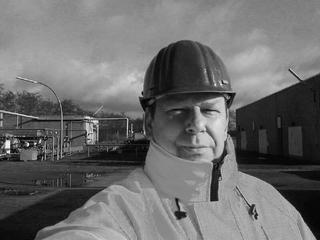
Six Sigma Unterstützung bei der Untersuchung und Fehleranalyse abweichender Auszugskräfte im Bereich der A- Säulenverkleidung PKW. Unterstützung bei der Ursachenanalyse von Qualitätsproblemen im Bereich der B-Säule PKW. Ausbildung von 24 Six Sigma Green Belts in Übereinstimmung mit den Anforderungen des ESSC und operational excellence. Die ausgebildeten und zertifizierten Green Belts konnten bisher € 1,2Mio. an Einsparungen realisieren.
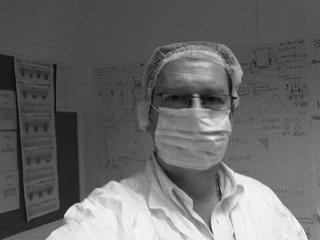
Six Sigma Black Belt Unterstützung der Cross Functional Task Force durch Einführung von Six Sigma Projektmanagement in Übereinstimmung mit der DMAIC- Prozessverbesserungsmethode zur Verbesserung der Ausbringung und Reduzierung von Ausschuss. Steigerung der Ausbringung um 80%, Ausbildung von 15 Green Belts.