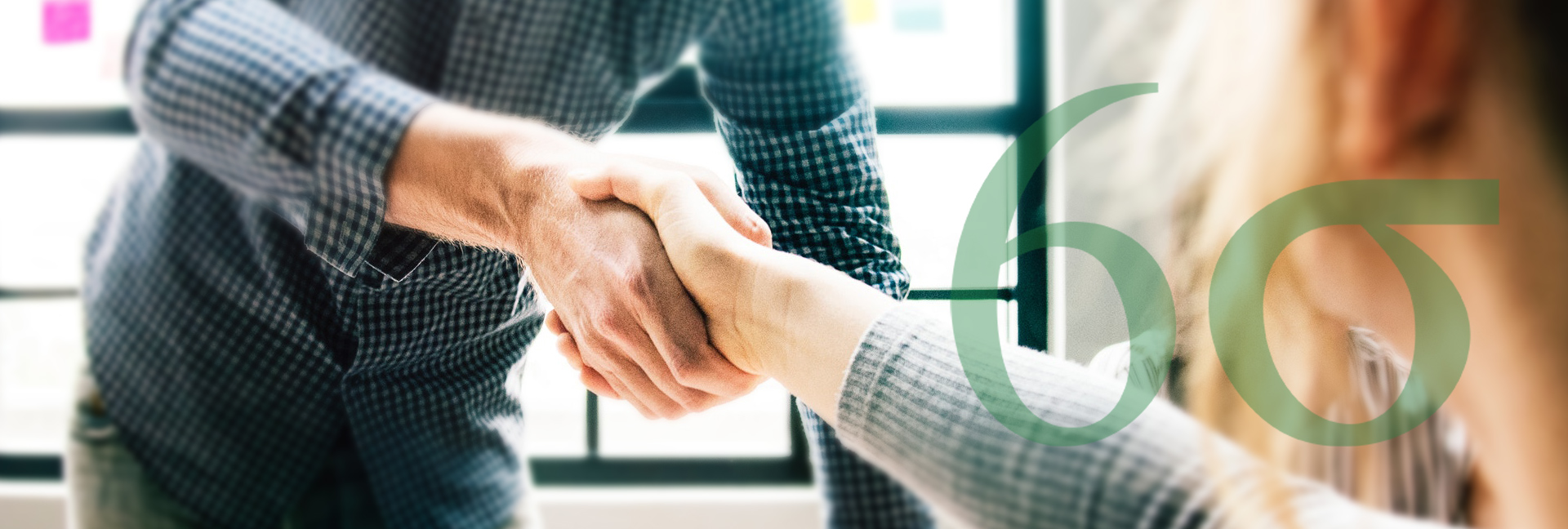

References of our activities
Being “Hands on” means to us, to be in the thick of things and not mere by-standers!
Industry sectors
Aviation
Automotive
Mechanical engineering
Plant construction
Logistics
Company examples
General Motors
DeLaval Ltda. (Argentina)
Mercedes Benz
Volkswagen
Porsche
Boshoku Automotive Europe GmbH
Toyota, DeLaval Services GmbH
SELL GmbH
Magna Electronics Europe GmbH
GDF Suez, DeLaval Ltda. (Brazil)
Asco Deutschland GmbH
IBS Filtran GmbH
Selection of some Reference-Projects
Implementation of "LEAN logistics" in a global distribution centre, which is part of a global leading packaging manufacturer, to support the implementation of a group-wide production system in order to double the company within the next 5 years.
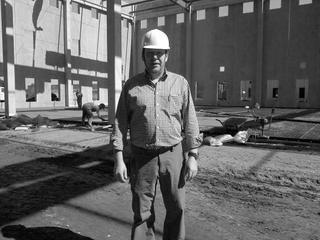
Performance of basic Six Sigma Lean Production training for all operational and administrative employees for better understanding of the methods and tools as well as their intention and objective.
Analysis and improvement of all operational logistics processes by applying Six Sigma Lean production tools and methods. Hands-on optimizing of the value stream (e.g. KAIZEN, SPC) in collaboration with employees and managers at all levels.
Implementation of 5S, "visual controls" KPI's and a significantly improved capacity planning and forecasting system, coupled with well advanced visibility of the operational and administrative process indicators. Analysis of current Warehouse capacity with regard to the desired strong growth of 100% within 5 years. The project will be handed over to internal staff which has been Six Sigma LEAN trained by PACT Process solutions.
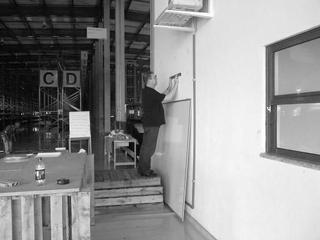
Six Sigma Lean Master support for creating a baseline for determining cost savings potential in connection with an investigation on changing the organizational structure for production and maintenance. In addition to various opportunities for organizational changes, significant savings were determined as well.
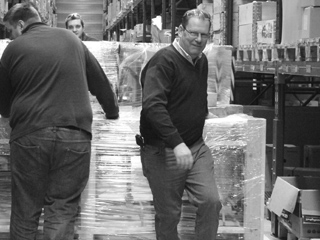
Six Sigma Lean production support of a global logistics and warehouse team in order to ensure proper design and project execution of a brand new Warehouse to be build up (green field) in Campinas / Brazil. Main tasks are to support the Layout planning and value stream mapping in accordance with Lean logistics, to provide the required Lean equipment and tools, to prepare visual controls and a key performance measurement system. The planning and preparation process of the physical move is also part of the project.
5 Waves of six sigma green belt training performed. Total amount of 45 green belt candidates trained (upper mgmt.; middle mgmt. & employees) - 29 certified, savings approx.€900K.
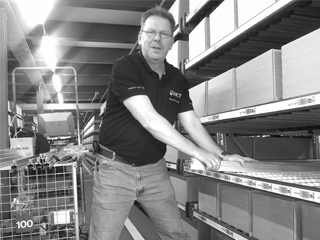
The training was performed in accordance with the requirements of the ESSC and "operational excellence". Projects were accomplished in the warehouse operation as well in the business administration.
Implementation of Lean Production for Repair and Overhaul of Auxiliary Power Units and Propulsion Engines - reduction of turn times by 58%, productivity improvement by 8%, Lean benchmark.
Small parts store optimization project re-organization, optimization and introduction of gravity flow racks, relocation of packing station and optimization of small parts distribution center form batch work to one piece flow, productivity 20% to be verified over time - on time, on target & within budget.
Lean kitting part 2 – cell production, 20% productivity target not yet fully achieved but getting much closer, on time & within budget.
Lean outbound project – flow, safety, ergonomics, motivation, productivity 38%, on time, on target & within budget.
Sigma Master Black Belt support of an internal Task Force Team to guide and support the root cause analysis of unnecessary field escapes of a diesel engine control unit. Investigation and project documentation as well as progress control meetings with customers and suppliers. The root cause was detected and confirmed within a very short time.
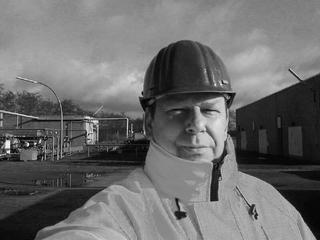
Six Sigma MBB support to investigate and analyze the root cause for the deviation and failure mode of differing extraction forces in the area of the A-column interior lining for a superior automotive manufacturer. Additional support in order to analyze the root cause of some significant quality problems in the area of the B-column interior lining for the same automotive manufacturer. Training and on site mentoring of 14 Six Sigma Green Belts in accordance with the requirements of the ESSC and operational excellence. Savings of more than €1200K were achieved.
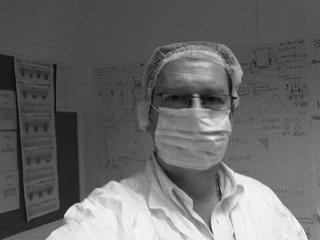
Six Sigma Master Black Belt support of cross functional task force by implementing Six Sigma project management in accordance with the DMAIC -process improvement methodology for improvement of first throughput yield and reduction of defects.
Improvement of first throughput yield by 70%, training of 15 Green Belts.